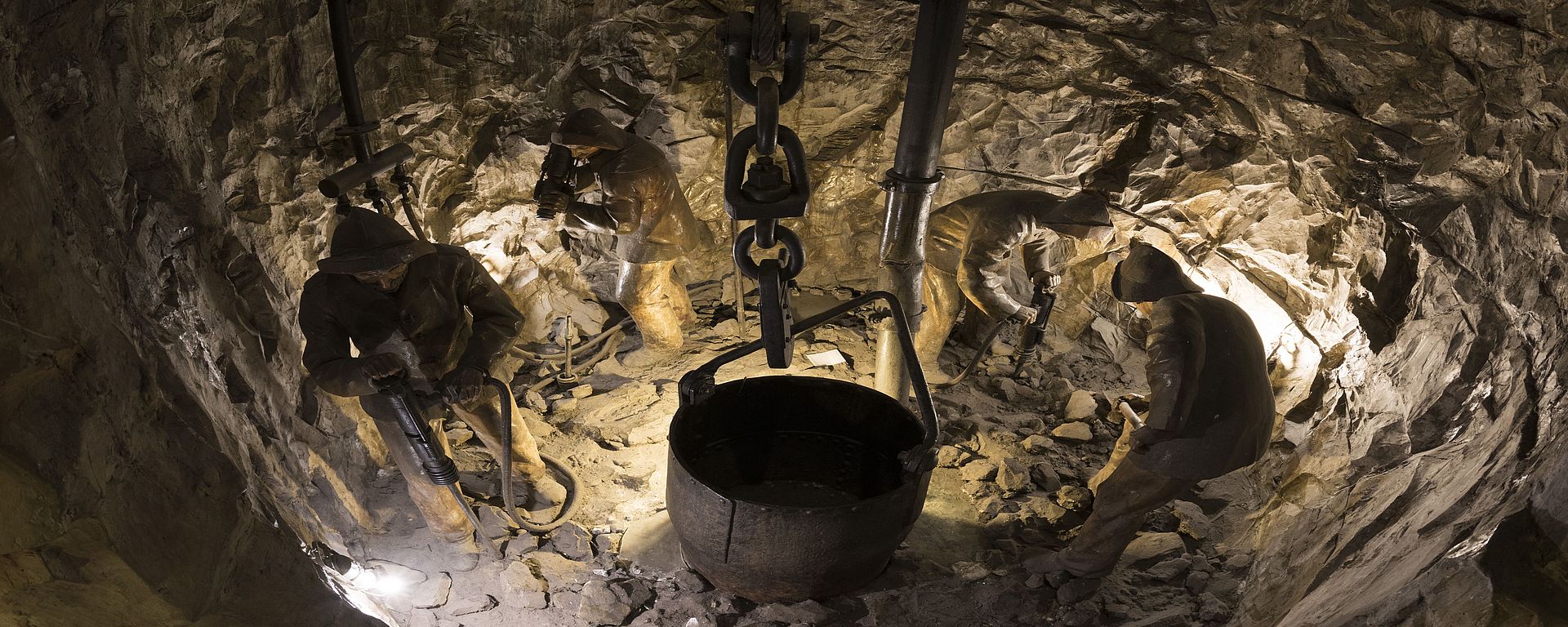
Photo: Deutsches Museum | Christian Illing
Materials Energy Production
Mining – Exhibition themes
Mining and processing – extracting and refining resources. This exhibition explores the following topics and contents:
Pit bank. Photo: Deutsches Museum
Shaft construction and transportation – journey into the depths of the earth
For centuries, hammers and picks were the only tools used in the mining industry. It was only in the 17th century that blasting with gunpowder was developed. In the first shaft, you can see a miner using a hammer and gimlet to make blast holes. This is followed by the huge drill head of a Kind-Chaudron drilling system. This was used for the first time in the 19th century to save time when drilling. Opposite, you can see miners sinking a shaft.
The pit bank is set up at the top of the shaft and is used for emptying the skips and bringing in material. Nearby is the system’s drive motor, the water wheel. The exhibited pit bank is an original from the Rammelsberg ore mine in Goslar, Germany from the 19th century. A “gravity loader” is emptying a skip into a cart. Next to this, the replica of a functioning man engine from the same period shows an energy-saving means of transport for the miners of that time. The bottom landing is at the bottom of the shaft, where the vertical hoisting meets the horizontal haulage. This is followed by the replica of such a bottom landing from the mine in Hausham/Upper Bavaria, Germany, around 1925.
Ore extraction with a hammer and pick. Photo: Deutsches Museum | Christian Illing
Historic ore mining – grappling with rocks and water.
From the stone age until the 17th century, miners worked with hand tools. At the beginning of the exhibition area, you can see a “hewer” with a hammer and pick kneeling at the end of a 3m long tunnel – the average annual performance of a miner in a hard rock wall. What can be done when the rock is very hard? Fire-setting is an old technique for breaking up or blasting hard rock, as can be seen in a scene from the Rammelsberg mine in Goslar, Germany.
The ingress of water in pits has always posed a risk. Water pumps were already being used in the ancient world. You can see a functioning replica of a rag and chain pump from the 16th century: a treadwheel drives an endless chain with leather balls, which transports the water above ground through wooden tubes. The actual ore excavation is shown using the stoping of the 1920s as an example. The excavation takes place from the bottom to the top. Pneumatic drills set the drill holes for the “blasting”, the use of explosives.
Photo: Deutsches Museum | Christian Illing
Surface mining – the mining industry of the past and the future?
Mining undoubtedly began with surface mining. Apart from flint, ore was also excavated by surface mining. Today, around 70% of the global extraction of ore and coal come from surface mining, as do the vast majority of raw materials from the non-metallic mineral sector.
The largest surface mines in Germany are used for the extraction of lignite and are in the Rhineland, in the Leipzig region and in Lusatia. The model of a modern lignite surface mine in the centre of the exhibition room illustrates the technology of surface mining. The establishment and development of a surface mine require a lot of space and have an influence on the landscape and the groundwater. In some cases, entire communities have to be relocated. Surface mining is controversial. Recultivation, the restoration of a near-natural condition, is very important to the German lignite mining industry today.
Wieliczka rock salt mine Photo: Deutsches Museum | Christian Illing
Salt mining – wet and dry
Salt has been mined since the Stone Age. At the entrance, a wooden slide is exhibited. In the Alps, miners used such a slide to enter the mines up until the 17th century. When you reach the bottom level, you will see in front of you a cavern that is apparently filled with water, a sink works. Water is introduced into this hollow space and gradually dissolves the salt from the rock. This principle of wet mining is still used today.
In dry mining, the salt is generally extracted during the chamber construction. Large, self-supporting cavities are created in the process. One such large space is opening up in front of you. The extraction of rock salt in the Wieliczka salt mine near Krakow, Poland (18th century) is depicted. Finally, there is a leap in time into an excavation chamber of a potash mine circa 1925. As in ore mining, two miners are preparing blast holes here. Potash has been mined in Germany since the end of the 19th century and is an important raw material in the fertiliser industry.
Pitch coal mining in a semi-steep seam. Photo: Deutsches Museum
Pitch coal mining – a Bavarian specialty
Pitch coal was only used for domestic fuel. Immerse yourself in the poorly lit scenes that represent Upper Bavarian pitch coal mining around 1900 and follow an approximately 1m high bed of coal, the seam, to a low working room, the coalface. There, miners lie or crouch and laboriously perform their work. On the one hand, coal is broken; on the other hand, rocks are brought in as stowing material. When you reach the bottom layer, you will be met by a pit pony that is pulling a tub to the nearest bottom landing. There, one such cart is waiting in the cage to be transported to a main haulage level, from where it will get to the surface, to the pit bank. At the end of the tunnel, you can assure yourself, by glancing into the stables, that the pit ponies are well cared for.
Coal mine, around 1950 (scene): in the 1950s coal mine, a coal plough (centre left in the picture) breaks the coal loose and the double chain convey transports it to a conveyor belt. Photo: Deutsches Museum
Bituminious coal of the 1950s – machines make the work easier
The extension of the tunnels in around 1900 ends in the bituminous coal mining of the 1950s. You will enter a blind shaft scene. A blind shaft ends beneath the surface. It follows a route that connects the hauling shaft to the tunnels that lead to the coal seam. There, you can see something that is unusual for coal mining to your right. A drilling jumbo is setting blast holes in the rock. Isn’t coal highly combustible? A specially developed process is used.
Your route continues to excavation in a “steep seam”; in the 1950s, the hewers still mainly worked with compressed air hammer drills both in very steep seams, as can be seen here, and in shallow seams. The use of machines is only possible in a seam with a smaller incline. At the end of the Bituminous Coal Mining area, this is depicted at a low face. No miners can be seen at the face. The work is done with machines, with a cutter, a hoist and a tipper for bringing in the stowing material.
The model of an ore processing system from the workshop of the Freiberg model builder Richard Braun reproduces in detail the machines and the necessary operations that are used to separate the valuable ore from the waste material. Photo: Deutsches Museum
Processing – crushing, screening, refining
At the end of the blind shaft scene, there is a jigger for transporting the raw material. What happens to these raw materials when they leave the mine? You can find the answer in the Processing area. Here, you can see how ore and coal are separated from waste rock and finally further processed in a smelting process or used as a source of energy (coal). Salt also goes through processing procedures. Salt is obtained from liquid brine through evaporation. The various separation processes take place through grading and sorting processes, which the exhibition explains with the help of models, demonstrations and dioramas. The Coal Refining area deals with the subject of coal as a source of energy and a raw material in its various forms. The exhibition currently ends here.
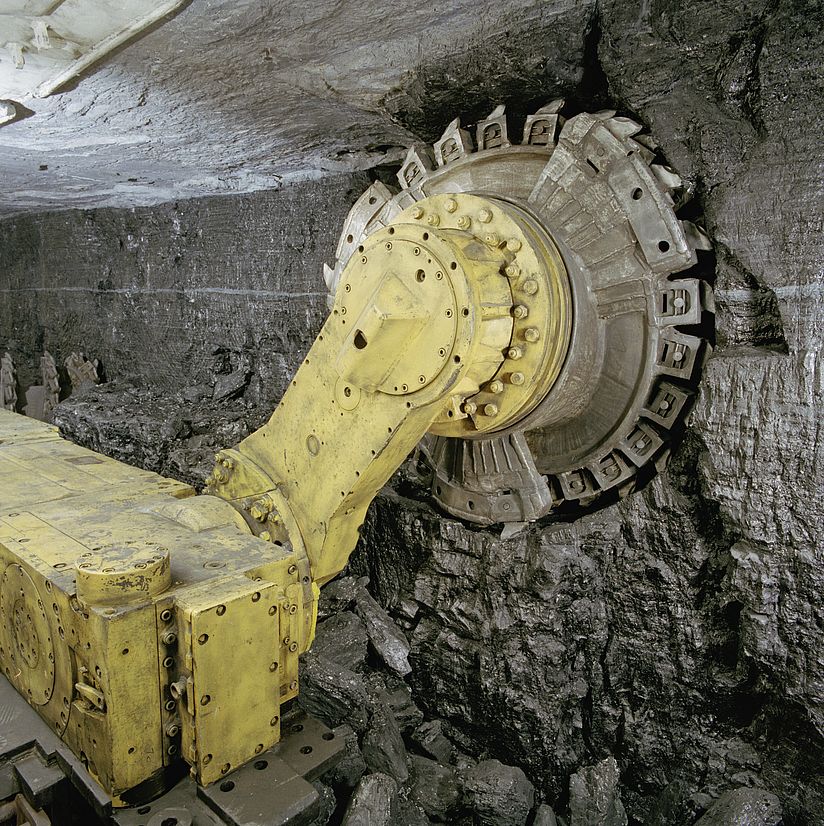
Drum shearer, 1981 (original): in a modern bituminous coal mine, the drum of a drum shearer, which is equipped with a pick, cuts the coal out of the seam. A chain conveyor runs under the machine and transports the extracted coal to a loading facility. The second drum can be seen in the background on the left. Photo: Deutsches Museum
Modern mining – on the way to automation (currently closed)
This area of the exhibition presents bituminous coal and ore mining since the 1970s. Many operations have been mechanised and automated. First, you will enter a spacious tunnel in a bituminous coal mine. An overhead monorail for the transportation of people and materials leads to an operating point at which an efficient machine unit consisting of a double drum shearer, a face conveyor chain and hydraulic shield support can be admired. The shearer strips off the coal. It is taken away by the conveyor chain in a continuous process. The shield support can be moved forwards (move forwards) completely automatically with the help of control technology (an integrated chain conveyor with coal plough or drum shearer) and thus bring down the rock mass behind it.
Finally, you will go through the ore chamber construction. The most important work processes in modern ore and salt mining are shown here with the help of large machines: drilling blast holes, filling the drill holes with explosive and carting away the raw materials with a diesel-powered wheel loader.